Understanding the Basics and Applications of Plastic Extrusion in Modern Production
In the realm of modern-day manufacturing, the method of plastic extrusion plays a critical function - plastic extrusion. This intricate process, entailing the melting and shaping of plastic through specialized passes away, is leveraged throughout various markets for the production of diverse products. From vehicle parts to durable goods product packaging, the applications are huge, and the potential for sustainability is similarly impressive. Deciphering the basics of this procedure reveals the real convenience and potential of plastic extrusion.
The Basics of Plastic Extrusion Process
While it may appear complex, the principles of the plastic extrusion procedure are based upon reasonably uncomplicated principles. It is a production procedure wherein plastic is melted and afterwards shaped right into a continual account via a die. The raw plastic product, frequently in the form of pellets, is fed into an extruder. Inside the extruder, the plastic is subjected to heat and pressure, creating it to thaw. The molten plastic is then forced via a shaped opening, referred to as a die, to form a long, continual item. The extruded item is cooled down and then cut to the desired size. The plastic extrusion procedure is thoroughly utilized in various industries due to its adaptability, cost-effectiveness, and performance.
Various Kinds of Plastic Extrusion Methods
Building upon the fundamental understanding of the plastic extrusion process, it is needed to explore the numerous techniques involved in this production method. The 2 key techniques are profile extrusion and sheet extrusion. In account extrusion, plastic is thawed and developed right into a continual profile, commonly made use of to create pipelines, rods, rails, and window frameworks. On the other hand, sheet extrusion develops huge, level sheets of plastic, which are generally further processed into products such as food product packaging, shower curtains, and auto components. Each method needs specialized machinery and accurate control over temperature and stress to ensure the plastic keeps its form during cooling. Recognizing these strategies is crucial to using plastic extrusion efficiently in modern production.

The Role of Plastic Extrusion in the Automotive Industry
A frustrating bulk of components in modern vehicles are items of the plastic extrusion procedure. This process has transformed the automobile industry, changing it into a more reliable, cost-efficient, and versatile manufacturing sector. Plastic extrusion is mainly used in the manufacturing of different vehicle parts such as bumpers, grills, door panels, and control panel trim. The process provides an uniform, consistent result, allowing producers to generate high-volume get rid of fantastic accuracy and very little waste. The agility of the extruded plastic components adds to the total decrease in lorry weight, enhancing gas effectiveness. The longevity and resistance of these components to warm, cool, and impact boost the longevity of vehicles. Hence, plastic extrusion plays a critical function in automotive manufacturing.
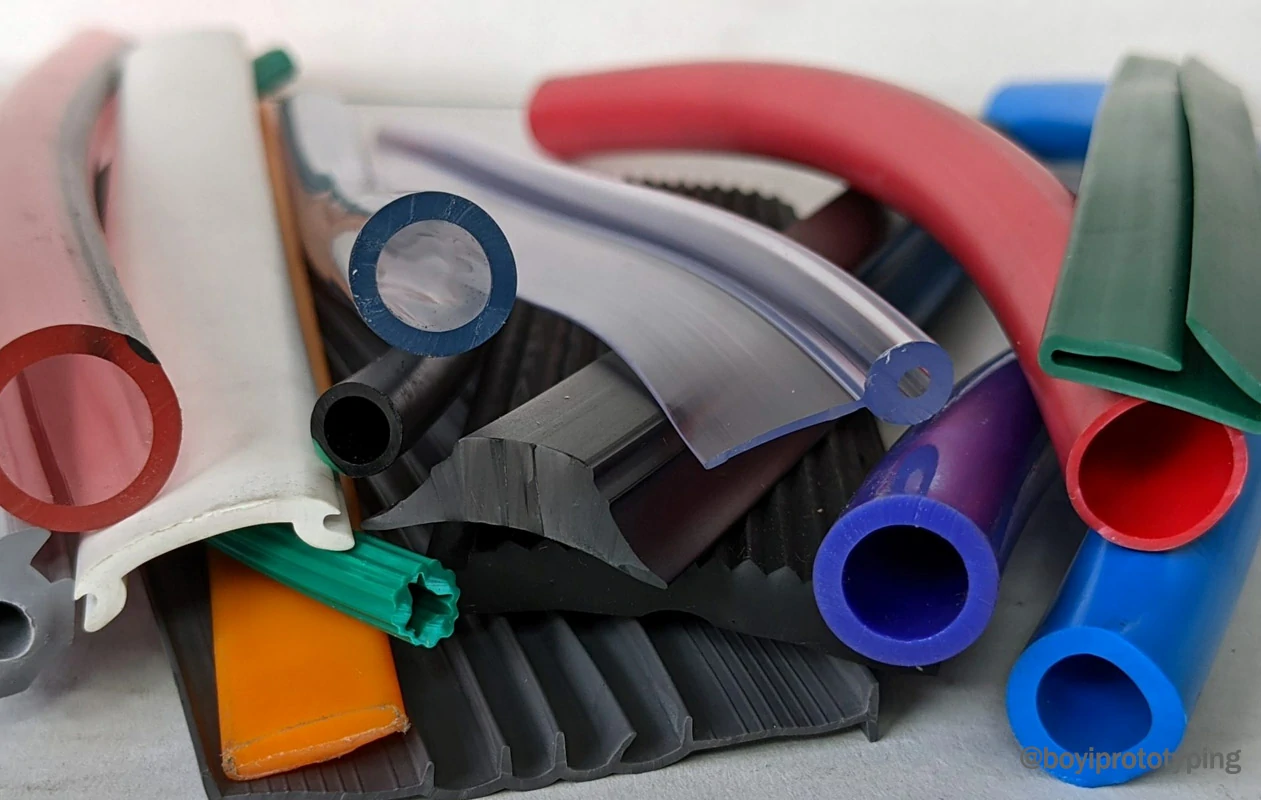
Applications of Plastic Extrusion in Durable Goods Production
Past its significant impact on the automotive industry, plastic extrusion proves equally effective in the world of customer items making. The convenience of plastic extrusion permits makers to create and create complicated shapes and sizes with high precision and performance. The adaptability, flexibility, and cost-effectiveness of plastic extrusion make it a favored option for numerous consumer items makers, adding dramatically his explanation to the market's growth and innovation.
Ecological Effect and Sustainability in Plastic Extrusion
The prevalent usage of plastic extrusion in producing invites analysis of its ecological ramifications. Effective equipment reduces energy use, while waste administration systems reuse scrap plastic, decreasing raw product needs. Despite these enhancements, additionally technology is needed to mitigate the environmental footprint of plastic extrusion.
Verdict
To conclude, plastic extrusion plays an important duty in modern-day production, specifically in the auto and consumer items sectors. Its flexibility permits the manufacturing of a vast array of parts with high accuracy. Its possibility for recycling and development of eco-friendly products provides a promising great site method in the direction of sustainable practices, thereby resolving environmental concerns. Recognizing the fundamentals of this process is vital to enhancing its advantages and applications.

The plastic extrusion procedure is thoroughly utilized in different markets due to its versatility, cost-effectiveness, and efficiency.
Building upon the standard understanding of the plastic extrusion procedure, why not try these out it is required to explore the numerous methods included in this manufacturing approach. plastic extrusion. In contrast, sheet extrusion creates huge, flat sheets of plastic, which are usually further refined into items such as food product packaging, shower curtains, and auto components.An overwhelming bulk of parts in modern-day automobiles are products of the plastic extrusion process
Comments on “Plastic extrusion for intricate profiles and custom designs”